射出成形、初めての樹脂や初めての金型(成形品)ではなかなか一回でうまくいくことは少ないですよね。出来上がった成形品を見てみると、表面になにか模様のようなものがみえること、ありませんか?
私は何回も経験しています(笑)
その中で、フローマークではなく、艶や光沢のムラを目にしたことはないでしょうか?この記事では、射出成形の艶ムラの原因とその対策について紹介していきます。
射出成形の艶ムラの原因
艶ムラの主な原因は、
- 流動バランス
- ガス抜き
- 肉厚差
- 金型温度
の4つになります。
それぞれ、なぜこれらが原因となって艶ムラが発生するのかを説明します。
その前に、簡単に艶ムラについて整理しておきましょう。
艶ムラとは
超シンプルにいえば、艶ムラとは、金型から転写された表面状態の差のことです。
光沢ムラともいわれますね。
色むらに関してはまた別の不良になります。
金属の表面に木目や岩目など様々な模様をつける金属加工がありますが、これをシボ加工といいます。
シボの種類によっても差が生じますが、シボの転写で起こる表面状態の差も艶ムラ、光沢ムラといいます。シボの場合は、深い方が艶ムラは目立ちにくくなります。
この記事ではこういった不良を「艶ムラ」で統一します。
それでは、主な4つの原因について解説していきます。
肉厚差による艶ムラ
まず、イメージしやすいのは肉厚差ですね。
成形品の中で、程度の差はあれ、肉薄な部分と肉厚な部分が存在するはずです。その厚さの差、すなわち肉厚差が原因となり、艶ムラが生じます。
もう少し細かく突っ込むと、肉厚であればあるほど転写で必要な圧力が高くなり、長い時間が必要になります。
それぞれの肉厚の部分でそれぞれ適した圧力がかからないことが十分考えられますので、それが転写の程度の差につながり、結果として艶ムラが生じてしまうのです。
また、肉厚差によってヒケが生じ、その結果艶ムラのように見えるということも起こります。
流動バランスによる艶ムラ
肉厚差にもかかわりますが、場所によって樹脂の流れやすい・流れにくいがどうしても存在します。
これによって、流動バランスが崩れてしまうことがあります。
具体的には、流動バランスが崩れた結果、樹脂が固まってしまう部分、固まり始めた部分、固まっていない部分が発生してしまい、それぞれの転写に必要な圧力が変わってきます。
その結果、艶ムラが生じてしまうのです。
ガス抜きによる艶ムラ
こちらの記事でガスベントのことを紹介しました。
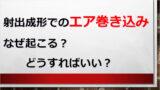
観点に言えば、金型内の空気の逃げ道のことです。
このガスベントがうまく機能しないか、不十分であった場合はガスが抜けません。
この結果、ガスがミクロレベルで成形品に入り込んでしまい、艶ムラが発生してしまうことがあります。
金型温度による艶ムラ
金型温度が想定通りにするのはかなり難しいです。
というのも、温調回路の位置や金型の中で傾斜部があったり、型開きのときに空気に触れたりするなど、厳密に金型温度を一定にすることは困難です。
つまり、金型内に温度勾配や温度の不均一部の発生し、場所ごとに蓄熱の仕方に差が生じてしまいます。
こうなると、温度が高いところの方が転写しやすくなるので、転写による差が生じ艶ムラとなってしまうのです。
射出成形の艶ムラの原因と対策5選【金型編】
主となる原因を4つ紹介しました。
ここからは、金型に絞って原因や対策を紹介していきます。
エアベント不足
金型の設計上、エアベントがなかったり、不十分だったりすると金型内のガスが抜けることができず、艶ムラにつながってしまいます。
「ガス抜きによる艶ムラ」というやつですね。
対策としては、十分なエアベントを確保し、しっかりとガスが抜けるように金型を修正しましょう。
ゲートが小さい
「流動バランスによる艶ムラ」の具体的なケースになりますが、ゲートが小さい場合も艶ムラが発生しやすいです。
ゲートが小さく、樹脂が流れにくいと必要な圧力も局所的に上がり、流動バランスが崩れてしまいます。
対策としては、ゲートを少し大きくなるように金型を修正しましょう。
スプルーやランナーが細い
ゲートと全く同じ理屈です。
ロスを減らすために細めにしたい気持ちは痛いほどわかりますが、不良が出てしまったら本末転倒です。
対策としては、スプルーやランナーを太めに修正しましょう。
キャビティの磨き状態が悪い
転写されるので金型そのものが悪ければそれ以前の話、というわけです。
金型を使用していく摩耗するため、メンテナンスは必須です。
きれいに磨けていなければそれがそのまま転写されてきれいな外観にはならなくなってしまうので、対策としては金型のメンテナンスになりますね。
キャビティ表面にデポジットがある
デポジット、要するに不純物が金型に付着しているという状態です。
そりゃ不純物あれば艶ムラどころかそれ以上の不良が想像できますよね。
対策としては、金型の清掃になります。
射出成形の艶ムラの原因6選【成形条件編】
続いては成形条件にフォーカスして原因と対策を紹介します。
成形条件なので、比較的すぐに試行できるので試すには先にこちらで対応するのがいいかと思います。
計量不足
そもそも樹脂が足らないという場合です。
樹脂が不足していれば艶ムラ以前に充填ムラ等で物性にも影響が出るので、成形品の重量測定できちんとモニタリングしてください。
対策としては、計量値を増やすことが有効です。
クッション位置が短い
クッション位置が短いと十分に保圧をかけることができません。
この状態では樹脂に適切な圧力をかけることができないので、艶ムラとなります。
対策はクッション位置を増やすようにして下さい。
クッション位置だけを大きな値にすると充填する樹脂の量が減ってしまうので、計量位置もその分大きな値にしてください。
クッション量に関してはこちらの記事でも紹介しているのでぜひ一緒にご覧ください。
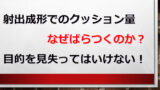
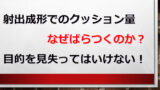
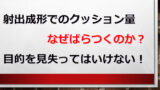
保圧が低い
クッション量でも触れましたが、十分に樹脂に圧力をかけられないことが原因で艶ムラが生じてしまうとお伝えしました。
クッション量が十分でも、保圧そのものが低すぎると結果的に十分圧力がかけられない条件となってしまいます。
ですので、そのような場合は保圧を高くしてください。
保圧時間が短い
同様に、クッション量が十分で保圧も適切であったとしても、保圧時間が短ければ十分に保圧をかけられていない状態となります。
1秒ずつ保圧時間を長くしたサンプルを作って、重量がサチるところを探して保圧時間を設定するようにしてみてください。
キャビティ表面温度が低い
キャビティの表面の温度がメーカー推奨の温度等の適切な温度でない場合、冷却のされ方に違いが生じてしまい、艶ムラにつながります。
私も普段は表面温度と温調機で金型温度をモニタリングしていますが、やはりできることなら内部をしっかりモニタリングしながら成形をしたいと思っています。
対策としては、温度をモニタリングできるようにするか、表面温度から表面状態の送還を取ることで条件を設定することになりますね。
樹脂の乾燥不足
樹脂の乾燥が不十分であれば、シリンダー内で気体となり、エア巻き込みが起こってしまいます。
詳しくはこちらで解説しています。
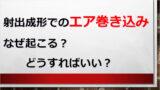
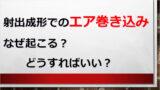
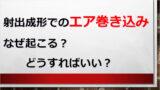
対策としては樹脂の乾燥を十分に行うようにしてください。
まとめ
今回は艶ムラにフォーカスして解説しました。
艶ムラの対策をしていたはずが、パラメータを変更したことで予期せぬ不良が起こってしまうかもしれません。
そのためにも、一つ一つ知識を身に着け、自分の中の引き出しを増やしておくことを心がけましょう(お互いに)。
まずは、艶ムラの主な原因4つと金型や射出成形での具体的な対策11個を整理しておくようにしときましょう!