消費者の目にとまる部品を成形すると、どうしても気になるのは外観ですね。
まあ、みえないところなら、多少は…という気持ちもわからなくもないですが、それでも見逃せないくらいの不良もあります。
そうです、ジェッティングです。
目をつむっていても外観不良がわかるんじゃないかってくらいの規模のものもありますよね。
そういう状態は健全ではないので、当然改善する必要があります。
この記事では、射出成形のジェッティングの原因について、メカニズムや対策もあわせて解説していきます。
射出成形のジェッティングの原因はこの3つ
ジェッティングの原因は主に射出速度金型温度流路の3つですが、その前に認識を統一しておきましょう。
ジェッティングとは
超簡単にいえば、ジェッティングとは成形品表面にくねくねした模様が表れる外観不良のことです。
ジェットフローという呼ばれ方もします。
ミミズが這ったような跡、などと表現しているテキストも多いですね。
私自身、実際に作ったことはないのですが、数ある不良の中でもかなり判別しやすいものだと思います。
ジェッティングの原因
では、ジェッティングの原因です。
ジェッティングの主な原因は前述の通り3つで、
- 射出速度が速すぎる
- 金型温度が低すぎる
- 流路が長い
のすべて、またはいくつかの組み合わせで起こります。
これらがなぜ原因になるかはメカニズムを理解すればかなりイメージしやすく、自然と対策も見えてくるはずです!
ジェッティングの発生メカニズム
簡単にいえば、固化した樹脂が混ざらずに残ってしまうためです。
これがオチだと思って、詳しく見ていきましょう。
金型に樹脂が入るとき、ノズルから樹脂が出てきますが、その樹脂は温度が低くなっています。
温度が低くなった樹脂が金型に触れて熱を奪われたり、勢いよく樹脂が飛び出して金型に触れるまでの時間が長かったりすると樹脂が飛び出した形のまま固化してしまいます。
イメージとしては、マヨネーズのふたを開けて、思いっきり握った状態です。
自己責任でやってみていただいてもかまいませんが、ものすごい勢いで吹き出しますよね(笑)
そういう状態で樹脂が固まったと考えてください。
ノズルから出た樹脂の温度は下がる一方なので、そのような形で固まると、そのままです。
あとから溶融樹脂が流れ込みますが、その形状から混ざり合うことはできず、押し出されて流されて化石のように形が残ってしまうんですね。
これがジェッティング発生のメカニズムです。
このメカニズムがわかれば、
- 勢いよく樹脂が出たらだめだな(=射出速度が速すぎたらだめだな)
- 急に冷えたらすぐ固まってだめだな(=金型温度が低すぎたらあかんな)
- 壁(金型)に触れずマヨネーズ(樹脂)が飛び続けたらそのまま固まるな(流路長すぎはNGだな)
とご理解いただけると思います。
これがジェッティングの原因とメカニズムです。
射出成形のジェッティングの解決方法
では、このジェッティングはどのようにアプローチしていけばいいかを紹介していきます。
主な対策は6つです。
6つのうち3つは成形条件に関する対策、残りの3つは金型を加工することでの対策です。
金型の加工は大変なので、まずは成形条件で改善を試し、うまくいかなければ金型を加工するという流れがコスト的にも手間的にも無難な順序だと思います。
【成形条件編】ジェッティングの対策3選
これは原因でも紹介したものと通じるものがあります。
射出速度を下げる
射出速度が速すぎてジェッティングが起こるのですから、至極まっとうな対策ですね。
しかし、遅ければいいというわけではありません。
遅すぎるとコールドスラグが発生したり、フローマークが発生したりします。
コールドスラグはこちらの記事でも紹介しているので、知らない場合は読んでみてください。
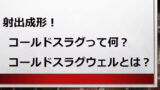
ジェッティングとフローマークは表裏一体な不良です。
射出速度が速すぎればジェッティング、遅すぎればフローマークとお考え下さい。
適切なラインは大事ということですね。
金型温度を上げる
こちらも射出速度と同様に、温度が低いのが原因なら上げればいい、というだけですね。
冷却効率に影響するので、様子を見ながら調整してみてください。
成形温度を上げる
温度が低くなるのであれば、最初からもっと熱を持たせておこう、という考え方ですね。
ですが、ジェッティングの対策で有効になる可能性は低いです。
こちらを優先的に行うのではなく、まずは射出速度や金型温度、これらの組み合わせで検討してみてください。
【金型加工編】ジェッティングの対策3選
では、金型での対策を紹介します。
金型の加工は手間もお金も時間もかかるので、できれば成形条件で何とかしたいところですよね。
湯だまり(ディンプル)を大きくする
湯だまりとは、樹脂を安定的に流すために設けられた肉厚になる部分のことです。
ディンプルとも呼ばれます。
これを大きくすれば、流れが穏やかになり、流動も安定する方向に進むので、対策の一つとお考え下さい。
ゲート径を大きくする
ゲート径が小さいとどうしても勢いよく樹脂が飛び出してしまいます。
ホースからでる水を想像してください。
そのホースの口を少しつぶすと、水は遠くまで勢いよく飛んでいくようになりますよね。
こんなイメージです。
ですので、ゲート径を大きくすれば、ホースの口を大きくするように樹脂の流れる速度は遅くなります。
しかし、ただ大きくすればいいというわけではなく、材料によっては別の外観不良の原因にもなりかねないので、慎重に検討してください。
ゲート位置や形状を工夫する
樹脂が勢いよく飛び出すのがよくないので、例えばゲート付近にピンを立てて、そこにあえてぶつけるというかんがえかたがあります。
こうするとジェッティングは起こりにくくなります。
流路を短くするようなイメージですね。
また、オーバーラップゲートやサブマリンゲートを採用するなど、ゲートの形状を工夫するのも方法の一つです。
このように、金型の形状を工夫することで解決する場合もあります。
ジェッティング対策のまとめ
対策一覧として、ここまで紹介したものをまとめておきます。
成形条件編としては、
- 射出速度を下げる(下げすぎ注意)
- 金型温度を上げる(冷却のされ方に注意)
- 成形温度を上げる(優先度低め)
の3つです。
金型加工編としては、
- 湯だまりを大きくする(樹脂の流動を安定化させる)
- ゲート径を大きくする(樹脂の飛び出る勢いを小さくする)
- ゲート位置・形状の検討(対策ピンやゲートの種類変更など)
の3つです。
樹脂や成形品の形状にもよって有効な対策は変わってくるので、成形品の外観をよく観察して対策方法を選んでください。
まとめ
今回は成形品の不良の中でも主張の激しいジェッティングに関して解説してみました。
技術者として、原因を知り、メカニズムを理解し、そのうえで対策をするのは非常に重要なことです。
今回は比較的イメージしやすい内容だったと思います。
基本的には一部分だけ先に固化するのを防ごうという考え方です。
何がいけないかを細分化して良品をバンバン作れる成形条件を導き出してください!